Retrofitting in the context of machinery and electronics refers to the process of updating, upgrading, or modernizing an existing system or equipment with new technology or features. This is often done to enhance performance, improve efficiency, extend the lifespan of the equipment, or comply with new regulations or standards. The retrofit process can vary significantly based on the type of equipment and the extent of the updates required. Retrofitting is a vital process in many industries, helping to keep older equipment relevant and functional in a fast-evolving technological landscape. It’s a sustainable approach that balances the need for modernization with the practicality of existing investments.
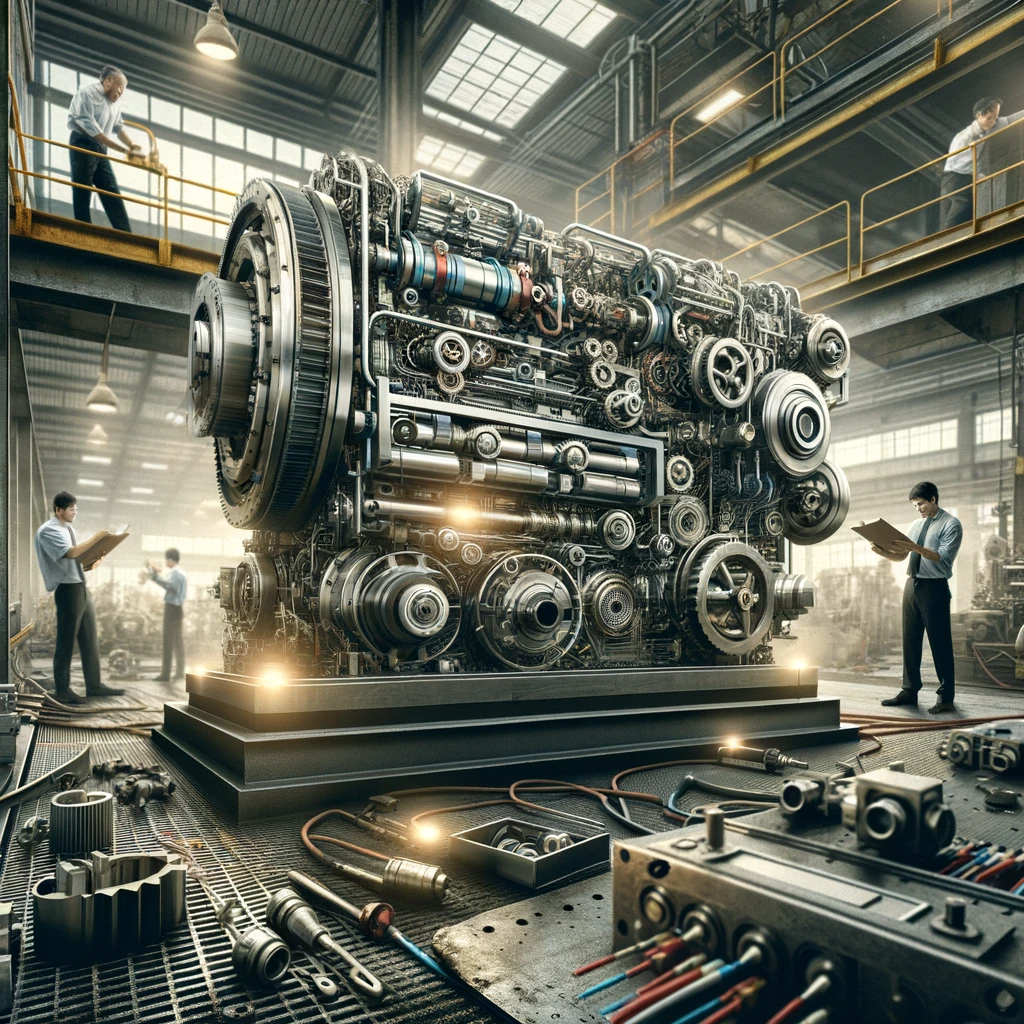
Process of Retrofitting
- Assessment: The first step is to assess the existing system to determine what upgrades are possible and necessary. This includes understanding the current capabilities, limitations, and the desired outcome of the retrofit.
- Design and Planning: Based on the assessment, a retrofit plan is designed. This involves selecting the appropriate technology, components, and designing how they will integrate with the existing system.
- Component Selection: Choosing the right components that are compatible with the existing system and will meet the new performance requirements.
- Installation: The actual process of installing the new components or systems. This may require partial or complete shutdown of the existing system.
- Testing and Commissioning: After installation, the system is tested to ensure that it operates as expected. Any necessary adjustments are made during this phase.
- Training and Documentation: Staff may need training on the new features or systems. Proper documentation is also provided for future reference and maintenance.
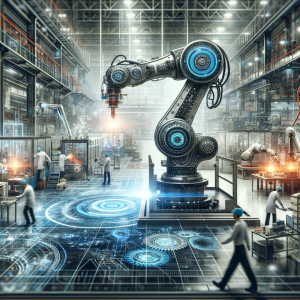
Benefits
Often more cost-effective than buying new equipment, especially for large or complex machinery.
Can significantly extend the lifespan of existing equipment.
Upgrades can lead to better performance, efficiency, and reduced operating costs.